Tire tread depth is an important factor of safety in the trucking industry. Maintaining the correct tire tread depth for commercial trucks is important, as it enhances longevity of a truck and reduces accident risk. It can also influence the vehicle’s grip and its ability to brake.
Understanding the importance of tread depth allows safeguarding the lives of drivers and other traffic participants. This is important for the commercial trucking sector. The regulatory bodies establish specific tire tread depth standards for commercial vehicles to ensure the compliance with safety standards.
The article includes the importance of tire tread depth, the DOT’ regulations, and practical advice on how to maintain your tires compliance.
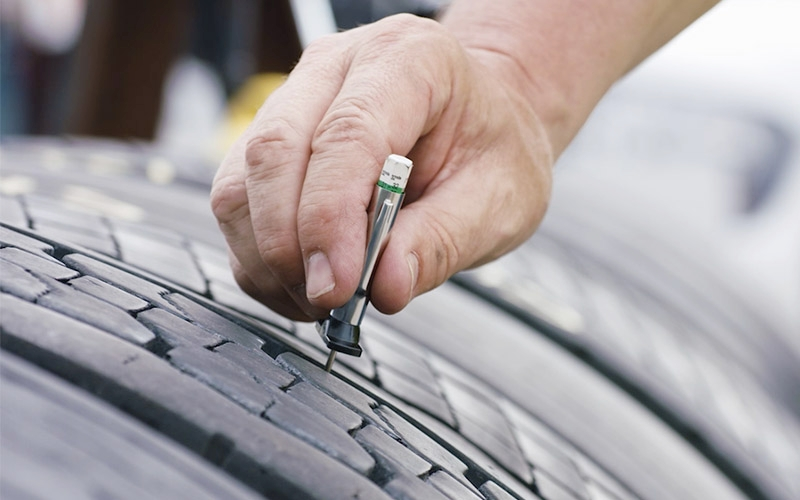
What is Tire Tread Depth?
Tire tread depth is the factor that refers to the safety and proper condition of a truck’s tires. It’s measured by the vertical distance between a tire’s rubber tread top to the bottom of the deepest grooves. This refers to a tire’s ability to maintain traction and prevent losing control of the vehicle.
New tires usually have a tread depth of 10/32 to 12/32 of an inch. Over time, the depth increases, impacting a vehicle’s performance. In particular, it affects a tire’s ability to channel water and grip the surface effectively. It leads to increased stopping distances and a higher accident risk.
In the trucking industry, tire tread depth is also a regulatory requirement. The Department of Transportation (DOT) sets specific regulations standards for tire tread depth. Thus, commercial trucks must have a tread depth at least 4/32 of an inch for steer tires and 2/32 of an inch for all other tires.
Regulatory compliance requires regular monitoring of tire tread depth. In addition, it’s important to check multiple points as uneven wear can lead to one side being more worn. Different factors, such as improper tire inflation, misalignment, or unbalanced loads, can cause uneven wear.
Moreover, adequate tread depth ensures the longevity and performance of the tires. Insufficient tread depth can compromise safety, wear out more quickly, and cause more frequent replacements. This can lead to a significant cost for trucking companies.
DOT Tire Tread Depth Regulations
DOT regulations provide guidelines that all commercial truck operators must follow. The aim is to ensure safety on the road. The rules mandate the minimum tread depth for commercial vehicles’ tires. This maintains sufficient traction, stability and road safety. Adequate tread depth is particularly important under challenging conditions, such as rain, snow, or uneven terrain.
Importance of DOT Tire Tread Depth Regulations
The DOT tire tread depth standards are important for several factors. First, tread depth impacts a tire’s grip on the road. Insufficient tread can lead to higher risks during driving, such as hydroplaning and a loss of traction. This can be dangerous for trucks, increasing stopping distances and requiring stricter control during maneuvers.
The next aspect is ensuring consistency and fairness in the trucking industry. With an established minimum tread depth, the DOT ensures an equal playing field for all commercial vehicles. This prevents operators from cutting corners by using worn-out tires.
DOT tire regulations also promote the sustainability and profitability of trucking operations. In particular, maintaining truck tire tread depth can improve fuel efficiency, as these tires have lower rolling resistance. This provides cost savings overtime. It’s beneficial for fleets that cover long distances.
The Consequences of Non-Compliance
Violations of the DOT tire tread depth regulations can lead to severe issues. The major risk is the potential for accidents. Tires with decreased tread depth can lose traction, increase stopping distances and reduce control.
Non-compliance also leads to legal or regulatory issues, such as fines and penalties. If a truck is found to have tires that do not meet the requirements, it can be placed out of service. Thus, it can’t continue transportation until the tire replacement. This usually results in delivery delays or higher maintenance costs. Moreover, it can damage the company’s or the driver’s safety score, which is a critical factor in maintaining contracts and insurance rates.
How to Measure Tire Tread Depth
Measuring tire tread depth is essential in maintaining compliance with DOT regulations and overall safety on the road. For truck drivers and fleet managers, regular checks of the commercial truck tire tread depth help avoid costly violations and delays.
Tools You Need to Measure Tire Tread Depth
Accurate measurements require reliable tools. The most common tools are tread depth gauge or a simple penny. The tread depth gauge offers more accurate results and are often used during regular inspections for compliance. At the same time, the penny test provides a quick and easy way to get an estimate of your tire’s condition.
Failure to measure tread depth correctly can result in inaccurate assessments, leading to potential safety hazards, costly fines, and legal issues.
Tread depth gauge
It’s a specialized tool designed to measure the depth of the grooves in a tire. Tread depth gauges aren’t expensive and easy to use. They provide precise readings to 1/32 of an inch.
This tool is crucial for anyone who is involved in commercial vehicles operations.
The key features of this method include:
- Precision. A tread depth gauge allows for measuring the truck tire tread depth with exact precision. Even a tiny difference can impact performance.
- Easiness. The tool has a simple design. Thus, it’s easy for drivers and maintenance personnel to check tread depth regularly.
- Affordability. Tread depth gauges aren’t expensive. Their low cost and high utility make them a valuable tool for any trucking operations.
- Durability. Most tread depth gauges are built to last as they’re made from durable materials. Longevity means a single purchase and provides years of reliable service.
- Versatility. As they’re primarily designed for measuring tread depth, some gauges have the additional features, such as the ability to measure tire pressure or the evenness of tread wear.
Steps to measure tire tread depth:
- Choose the right spot. You should measure the tread depth in the major grooves. Measurements in minor grooves can reduce the accuracy.
- Insert the tread depth gauge. Place the base of the tread depth gauge flat against the tire. Push the measuring pin down until it makes contact with the bottom. Ensure it is perpendicular to the tire surface, as it’s essential for an accurate measurement.
- Read the measurement. Once the gauge is in place, read the measurement on the scale. DOT requires at least 4/32 of an inch for front tires and 2/32 of an inch for other commercial truck tires. If the results are below these levels, the tire is considered out of compliance.
- Repeat the process. The tread depth needs to be measured at several points. Uneven wear can occur due to improper inflation or uneven weight distribution.
- Record the result. Keep a log of your tread depth measurements. It will help you track tire wear over time, plan replacements, and ensure compliance during inspections.
Penny test
This method isn’t very accurate. However, it provides a quick and easy way to obtain a general understanding of your tire’s tread depth. The test foresees the use of a penny with Lincoln’s head serving as the reference.
The method involves placing the penny into the tire’s tread groove with Lincoln’s head facing down. If you see all of Lincoln’s head, your tread is worn to 2/32 of an inch or less, which is the minimum tread depth required by DOT.
However, it shouldn’t replace regular measurements with a tread depth gauge, as it doesn’t provide accurate measurements.
This method is commonly used as it doesn’t require any special tools. Its advantages foresee:
- Simplicity. The penny test is the simplest way to define your truck tire tread depth. It requires only a penny to obtain a generated idea on your tires’ conditions.
- Accessibility. Pennies are common and easily available. Thus, the method can be used anywhere, without need for special tools. It makes the penny test suitable for quick checks on the road or during routine inspections.
- Cost-free. The penny test costs nothing beyond the penny itself. That’s why the method is a popular choice for drivers, especially on the road.
- Quick reference. The penny test provides fast results and an understanding of whether your tires comply with the legal limit or not. While it doesn’t provide the precise measurement, it can alert you to potential issues.
Steps to measure tire tread depth:
- Insert a penny into the tread groove. Place a penny into the tire’s tread groove with Lincoln’s head facing down.
- Assess the tread depth. If you see the whole Lincol’s head, the tread depth is less than 2/32. Thus, the tire doesn’t comply with the DOT minimum requirement.
DOT Regulations for Different Tire Types
The DOT tire tread depth regulations help ensure the safety and performance of various tires types. Different types have specific requirements under the safety standards.
The DOT tire tread depth regulations can vary depending on the type and the role of a tire in the truck’s operations. Still, maintaining the proper truck tire tread depth is essential in all cases, providing safety and better performance.
Regular inspections, maintenance activities, and compliance with regulations ensure your fleet’s reliability.
Steer Tires
Steer tires are the front tires on a commercial truck and have a significant meaning for steering and handling. Amid their importance, DOT has stricter tire tread depth regulations for these tires.
- Minimum tread depth. The DOT requires steer tires to have a tread depth of 4/32 of an inch. It’s mandatory as the front tires provide reliable grip and handling. Deep tread ensures better contact with the road, especially in adverse weather conditions.
- Inspection frequency. Steer tires should be checked more frequently than the others amid their critical role. Regular checks ensure the tread depth remains compliance, preventing potential safety hazards.
Drive Tires
Drive tires are located on the powered axles of the truck. They’re responsible for providing traction to move the vehicle. Thus, they also have specific DOT tire tread depth requirements.
Minimum tread depth. The DOT requires a minimum tread depth of 2/32 of an inch for drive tires. This is less than the standards for steer tires, however, it’s also crucial for maintaining traction. Sufficient tread depth ensures effective grip on the road, prevents wheel spin, and provides power transfer from the engine to the road.
- Importance of even wear. Drive tires can experience uneven wear due to the wight distribution. Driver and maintenance personnel can regularly rotate the tires and check the tread depth to ensure compliance with DOT tire regulations and extend tires lifespan. Uneven wear can result in reduced traction and increased risk of skidding.
- Impact on fuel efficiency. The proper truck tire tread depth also helps improve fuel efficiency. This allows more efficient operations and lower fuel consumption.
Trailer Tires
Trailer tires or free-rolling tires carry a significant portion of the vehicle’s load. They also have their own set of requirements.
- Minimum read depth. According to the DOT regulations, drive tires must have a minimum tread depth of 2/32 of an inch as drive tires. This provides load stability and safe braking. In sufficient tread depth can provoke poor handling, increased stopping distances, and higher blowout risk.
- Load management. Trailer tires are subjected to varying loads depending on the transported load. Adequate commercial truck tire tread depth helps distribute the load evenly, reducing the risk of tire failure and improving overall safety.
- Regular inspection. Since trailer tires are often out of the driver’s line of sight, they can be overlooked during checks. However, regular inspections ensure the compliance with the DOT tire tread depth standards.
Retreated Tires
Retreated tires are widely used on drive and trailer axels. They are recycled by applying a new tread to a worn tie casing. Thus, retreated tires are a cost-effective option for many fleets.
- Tread depth requirements. Retreated tires must comply with the tire tread depth regulations. In particular, they must have a tread depth of 4/32 or 2/32 of an inch depending on their placement.
- Quality issues. While retreated tires can be a cost-effective solution, it’s crucial to check provides and choose those who meet all DOT tire regulations. Poorly retreated tires can lead to premature wear, tread separation, and increased risk of blowouts.
- Usage restrictions. Retreated tires aren’t generally permitted on steer axels of commercial trucks. This restriction is part of the DOT safety standards.
Specialty Tires
Specialty tires are used on off-road vehicles, oversized loads, or specialized commercial vehicles. They have different DOT tire regulations, depending on their specific use.
- Custom tread patterns. Some specialty tires are designed with custom tread patterns for specific applications. This can include off-road traction or reduced rolling resistance for higher fuel efficiency. Still, they must comply with the minimum DOT tire tread depth requirement.
- Regulatory variances. The DOT tire regulations also include variations of exemptions based on the vehicle type and operating conditions. However, regular inspections are required in all cases.
Common Issues with Tire Tread and How to Address Them
Maintaining proper tire tread depth is not only DOT regulation. It’s also aspect that ensures safety and efficiency. However, drivers can cause several common issues on the road. We provide common issues and guidance on addressing them to keep your tires in top condition.
Uneven tread wear
Uneven tread wear is the most frequent issue. It can result from improper inflation, misalignment, or unbalanced wheels. This issue can shorten the lifespan of the tire and lead to non-compliance with DOT standards.
Causes:
- Improper inflation. Under or over-inflated tires can wear out unevenly.
In particular, under-inflation leads to faster wear of the outer edges, while over-inflation provokes faster wearing of a tire’s center.
- Misalignment. Misaligned wheels can cause the tires to wear unevenly. This mostly affects steer tires.
- Unbalanced wheels. Unbalanced wheels lead to vibration while driving, which can cause certain areas of tire to wear down faster.
To address this issue, you can follow the next steps:
- Check tire pressure. The correct tire pressure is crucial. Remember to check tire pressure regular to ensure all tires are properly inflated.
- Wheel alignment. Schedule and conduct regular wheel alignment and balancing services. This helps distribute the weight evenly across the tire surface.
- Rotating tires. Rotate tires to ensure even the wear out. This can extend their lifespan.
Cupping
Cupping or scalloping is an irregular tread wear pattern. This is characterized by high and low points on the tire surface. This issue can affect the handling of the vehicle.
Causes:
- Suspension problems. Worn or damaged suspension parts can cause the tires to bounce during rotation, leading to cupping.
- Unbalanced tires. This can cause cupping amid the uneven distribution of weight on the tire. You can prevent tires cupping by following the next steps:
- Inspect suspension. Inspect the suspension system for wear and damage. The inspection should cover shocks, struts, and other components. This will help you identify worn or damaged part to prevent cupping.
- Balance tires. Ensure all tires are balanced, especially after a tire change or rotation. This helps distribute the weight evenly.
Feathering
This issue occurs when the tread ribs develop a sawtooth pattern. It’s caused by improper toe alignment. Feathering can lead to premature tire wear and non-compliance with DOT tire regulations.
The leading cause of feathering is toe alignment. The tires aren’t pointing straight ahead. This causes the tread ribs to wear unevenly, creating a feathered pattern.
This issue can be prevented with this strategy:
- Check alignment. Conduct regular alignment checks. Proper toe alignment ensures the tires roll straight, ensuring even wear.
- Tire rotation. Regular rotate tire to mitigate the effects of feathering.
Tread separation
Tread separation is a serious problem when the tread begins to separate from the tire’s body. This can lead to tire failure. In addition, it pauses a significant safety risk and leads to severe penalties for non-compliance with DOT tire regulations.
Causes:
- Manufacturing defects. Tread separation can occur due to manufacturing defects, particularly in retreated tires.
- Overloading. Carrying loads that exceed the tire’s capacity can cause excessive heat buildup. This can lead to tread separation.
- Punctures or damage. External damage that aren’t repaired properly can also lead to tread separation.
The following steps can prevent this:
- Monitor the load weighs. Ensure that the truck’s load doesn’t exceed the tire’s capacity. Overloading can result in tread separation, affecting the overall performance and safety.
- Conduct inspections. Regularly check all truck tires, especially retreated ones, for signs of separation or damage. Early detection and repair can prevent tread separation and ensure the DOT tire tread depth remains compliant.
- Conduct repairs. Proper repairs of punctures or damages ensures the safety of the tires. Poorly repairs can lead to weak spots and tread separation.
Additional DOT Tire Regulations
In addition to DOT tire tread depth regulation, the DOT set other critical rules for maintaining the safety and operations efficiency. These DOT tire regulations are projected to prevent accidents and ensure safety on the roads.
In particular, DOT requires drivers to comply with:
- Tire pressure requirements. Maintaining proper pressure is essential for safety and compliance. Even a tiny disruption or violation can lead to uneven wear and tire failure. The DOT requires all tires to be inflated according to the manufacturer’s recommendations. This helps maintain the correct commercial truck tire tread depth and ensures the overall performance.
- Tire load ratings. Each tire has its maximum load rating, which indicates the maximum weight it can carry. Exceeding this limit can cause excessive wear, reducing truck tire tread depth. The DOT requires that all commercial truck tires must be rated for the load they carry. This regulation ensures the tires won’t be overwhelmed, as this issue can reduce safety.
- Retreated tire regulations. Retreading is a common way in the commercial trucking industry, as it allows extending the life of tires. The DOT sets strict regulations on their use. Retreated tires are permitted on the drive and trailer axles, but not on the front steering tires of commercial trucks. This regulation is based on the critical role of steering axle for vehicle control.
Conclusion
Maintaining proper tire tread depth is not just compliance with DOT rules. It’s a critical safety measure that prevents accidents and reduces operational costs. Regularly checks of tire tread depth can reduce the risk of blowouts, improve the vehicle’s traction and baking ability and enhance overall road safety.
Improper tire tread depth can result to non-compliance with DOT regulations or such issues as increased stopping distances and lower vehicle control. Overtime, it can also result in more frequent tire replacements and higher operational costs.
Regular inspections, proper measurements, and timely replacements can lead to significant benefits and reduced operational costs in the long run. Keeping an eye on your tire tread depth is an investment in safety and efficient performance.